Chapter 3
Occupational safety and health
– The industrial sector in Europe has become a safer place in the 21st Century, largely due to companies investing in digital technologies;
– Data collection allows to improve Occupational Health and Safety (OSH) and turning work environments into even safer places;
– When working away from the primary workplace employees must ensure the application of the company’s OSH policy.
– Smart sensors can be used for direct OSH improvements, ensuring health and safety standards are met in real time.
Digitalisation of industry has the potential to provide exponential benefits to OSH by removing workers from hazardous environments, the automation of dangerous tasks and the use of smart Personal Protective Equipment (PPE). And OSH can be even more improved by computer-based handling of large volumes of information as this can permit better planning of workforce deployment.
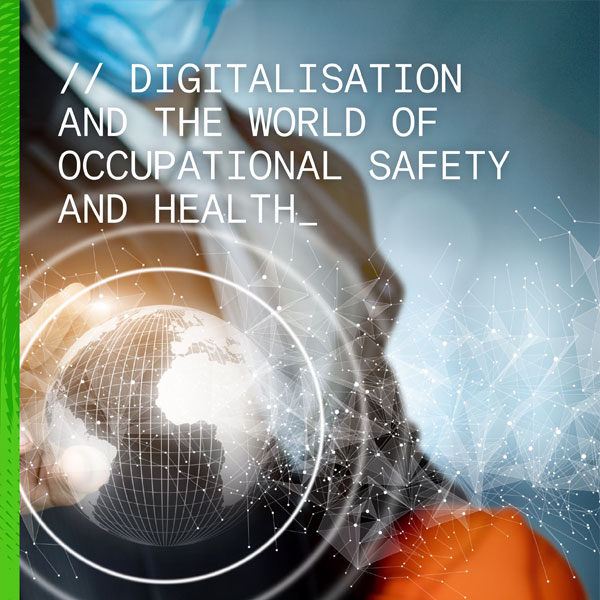
Digitalisation & OSH
Digitalisation is no longer new and its continuous its evolution throughout industry. Employers are continuously working on minimising challenges and risks that digitalisation at the workplace causes. Digital technologies, that already complement human labour, offer the possibility of creating a safer and healthier work environment. This publications zooms in on how to maximise the opportunities these digital technologies offers.
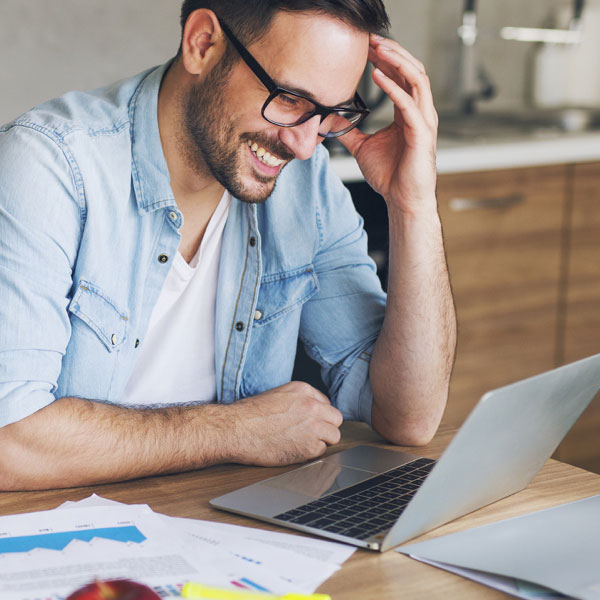
OSH & Regulation
With the Machinery Directive, there is legislation. But is it fit for future?
The next EU Framework on Health and Safety at Work post 2020 must anticipate the benefits of OSH and digitalisation. It must foresee the dissemination of best practices and the exploration of non-legislative measures. More EU funding must be allocated for research into the benefits of digitalisation on OSH, e.g. through the European Agency for Safety and Health at Work (EU-OSHA).
EU Regulation
The most fit for purpose directive to regulate the OSH area is the ,[object Object], The risk assessment and good guidance provide some of the best tools for employers to deal with any adverse effects of digitalisation within industry.
Data & safety
Improvements hinge on the collection and analysis of data at the workplace. Therefore we must find a balance between the activities of the employer and the data protection of the employee.
Touch and impact sensors detect when an employee is about to be injured and stop the machine before it happens.
Digitalised workplaces that make use of smart sensors, to e.g. measure real time noise levels, can set parameters with actionable data to fully ensure health and safety standards are met at all times.
Cybersecurity is often referred to in a context of protection of intellectual property rights and data protection. However, the advent of the Internet of Things (IoT) has left open the possibility of machines being hacked to destabilise the production process, potentially causing accidents.
Man-machine interaction
The OSH benefits of working in tandem with machines are clear. The disappearance of heavy and hazardous tasks is just one way. Employees are also experiencing healthier and longer working lives.
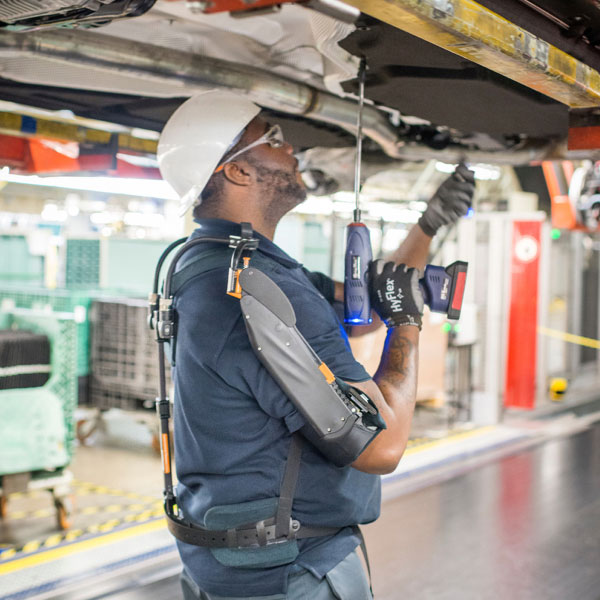
With AI making its way into manufacturing as the technology matures, cobots can become truly collaborative and work productively with their human colleagues. Employees can be fearful of the increased introduction of machines that work alongside humans. Therefore, cobotisation should be done in tandem with employees. This does not imply the acquisition of codetermination or information and consultation rights.
Through intelligent PPE, such as earmuffs allowing speech and normal sound, but which observe e.g. the sound of explosion and prevent it to get into the ear, we can reduce risks.
Issuing smart phones are not only restricted to the private life of the employee. In many cases it is a necessity to carry out their work
The analysis of job security reports which report on hazard locations, slips, or more serious accidents at work is a large task. The artificial language processing NLP (Natural Language Processing) is capable of processing thousands of digital documents, in any language. For large companies, this will produce a large database of incident and accident reports, across all of their sites.
Autonomous vehicles in factories are commonplace. Evidence is pointing towards a reduction in accidents. Training for their implementation remains key. The use of drones in industry is becoming more prevalent. One way in which they are being used to the betterment of employees OSH is moving items around production sites at height.
Exoskeletons: PPE in industry
Innovative Personal Protective Equipment (PPE) such as exoskeletons are worn directly on the body and can act like a second skeleton, i.e. as an external support structure for the body.
The BMW Group uses both upper-body and lower-body exoskeletons. The exoskeleton vest for the upper body strengthens the movement of the upper arms of people who have to carry out tedious tasks. The vest’s joints have an integrated mechanical spring support that gives arms greater strength. 24 of these exoskeleton vests are currently in use, 44 more will be added over the course of 2018.
Lower-body exoskeletons act as a chair-type support. This kind of exoskeleton improves workers’ posture and offers relief in carrying out assembly tasks that require crouching or remaining in other positions that might affect people’s occupational safety and health. On top of that, the leg support structure can transform prolonged standing into sitting and thus improve the comfort and flexibility of working conditions. The exoskeleton consists of movable splints that can be affixed to the legs or torso and locked in different positions. At present, 11 lower-body exoskeletons are used.
Value add by an app
The megatrends of Industry 4.0 and digitalisation both impact organisational OSH and protection. At its international locations, Voith has established a universal app for smart devices that actively engages employees in accident prevention.
To maximize its user friendliness the eVAP app was developed in direct cooperation with the employees. It now allows every employee to record observations quickly without complications, and to send the standardised report to Voith’s central HSE database.
Thanks to the global exchange of information, it enables fast action before accidents happen – across countries, production processes and business units. The employees benefit from the observations of their fellow workers around the world and due to its standardisation, the eVAP app offers great flexibility and transferability. This means that eVAP is seamlessly embedded in Voith’s overall occupational health and safety protection system.
Mobile & Remote working
Flexible workforce is one of the most important competitiveness factors for European industry.
Open-ended contracts represent the majority in the manufacturing and technology-based industries. Flexible forms of employment however, allow employers a margin to deal with fluctuations in demand and adding rightly skilled workers for periods when orders diverge from ‘normal’.
Challenges remain in the application of OSH legislation. Supervising working environments outside the employees’ normal place of work is difficult. Ensure good guidance and best practice to control risk is the solution.
There are factors outside of the workplace, or traditional second place of work, where OSH practices simply cannot be applied and controlled. It is therefore imperative that employees who are engaged in this type of work are given guidelines to control risk, rather than stringent rules which cannot be implemented.